Have you ever considered and wondered how golf clubs are made? No golfer would want to play with a below-average performing club.
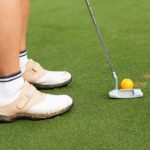
The golf clubs you use are probably the most crucial aspect when it comes to playing the sport. That’s why we go to lengths in enhancing the condition of our clubs.
As we focus on playing, this can be a matter that we don’t put much attention into.
A Close Look Into How Golf Clubs are Made
Since the game’s inception, golfers have continually found ways to upgrade their playing equipment.
From wood to metal to titanium materials, there is no doubt that we’ve come a long way with improving the game.
Furthermore, from manually making the clubs by hand, more and more manufacturers are utilizing technology in creating world-class clubs.
Indeed, the designing and manufacturing process of golf clubs is an art and science.
The latest automated and computer-aided machine is changing the way how are golf clubs manufactured.
Raw Materials
How are golf clubs made? First, let’s start with the raw materials. As you may now know, there are various types of clubs.
With each different club, the materials used on how are golf clubs manufactured differ.
Club manufacturers use a wide variety of materials for different types of clubs and various parts of the club itself.
Here are some of the most common materials used in how are golf clubs made:
- Metal
- Wood
- Stainless steel
- Aluminum
- Titanium
- Carbon graphite
- Carbon steel
- Zinc
- Plastic
- Ceramics
- Composites
The materials used on how golf clubs are made usually take mechanical properties into consideration.
These properties are strength, impact resistance, density, formability, friction, damping, etc.
Common Materials Used for Golf Club Parts
Here are the commonly used materials for each club parts on how are golf clubs made:
Club Head: Driver/ Wood Club
- Stainless steel
- Titanium
- Carbon graphite
- Aluminum
- Wood (usually persimmon, laminated maple, and other exotic woods)
For oversized metal woods, manufacturers usually fill it with synthetic polymer foam. Meanwhile, face inserts may be made of materials such as zirconia or titanium metal matrix ceramic.
For wooden club heads, manufacturers soak or coat it in preserving oil with a synthetic finish. This way, the club is protected from moisture, which can cause damage.
Club Head: Iron/Wedge Club
- Stainless steel
- Titanium
- Chrome-plated steel
- Tungsten
- Beryllium nickel or copper
- Zinc
- Combination of materials
Club Head: Putter
For putters, it can be made of the same materials as the irons.
However, it also makes use of softer materials such as aluminum or bronze. The reason being is that the impact velocity is relatively slower when you’re putting.
Shafts
- Stainless steel
- Aluminum
- Chrome-plated steel
- Titanium
- Carbon, boron, or graphite fiber-reinforced epoxy
Grips
- Molded synthetic rubber
- Wrapped leather
When it comes to regripping, it used to require the use of toxic and flammable solvents.
The reason behind this is that the solvent material activates the adhesive with a vise to force the grip on.
However, nowadays, the more common materials used for regripping are double-sided tape and water-activated adhesive.
Hosel
If you don’t know what a hosel is, this is the club’s part where the shaft attaches to the clubhead. Modern hosel designs weigh little in mass to lower the club’s center of gravity.
Think of it as a socket where the shaft slides into and then secured with epoxy.
Ferrule
Ferrules are usually black in color and have attached colored trim rings.
It’s often a decorative element but can also serve as a securing mechanism for the hosel and the shaft. Manufacturers typically use plastic in creating ferrules.
Design Rules
Are there any rules on how are golf clubs made? The standards for the design of golf clubs mainly focus on dimensions, according to the United States Golf Association (USGA).
Here are the dimension restrictions on how are golf clubs manufactured:
- The shaft of the club must measure at least 18 inches or 457mm in length.
- The head’s heel to toe distance must be higher than the head’s face to back distance.
- The grip’s cross-sectional dimension must not exceed 1.75 inches or 45mm in any direction.
- The most important rule when it comes to how golf clubs are made is: the construction of the club should not be different from its traditional and customary form.
By now, you are more knowledgeable in the design, materials used, and the construction of how golf clubs are made. Now, it’s time for the actual manufacturing process.
The Manufacturing Process
Most manufacturers usually make golf clubs using two distinct manufacturing processes. These are by casting and forging.
Here are the differences between how golf clubs are made depending on the process followed:
Casting
The casting process of manufacturing golf clubs typically makes use of liquid metal.
This molten material is poured into a mold of a golf club. After the metal has hardened, the craftsmen will break the mold and then process the clubhead.
Casting allows manufacturers to be flexible and creative in their process.
It gives them the ability to push the weight outside the head and prevents the possibility of twisting on off-center shots.
It’s no wonder why casting is the most popular method in manufacturing golf clubs—the number ranging around 90% of golf clubs made.
Here’s a guide on cast club make-up:
- 17-4 stainless steel: 17% is chromium, and 4% is nickel
- 431 stainless steel: 25% softer than the 17-4 stainless steel variant
While 17-4 is strong and durable, the 431 has a slightly better “feel.”
Forging
On the other hand, the forging process involves crafting the golf club from one piece of solid metal. Craftsmen would then heat and hammer it until it reaches its final shape.
Since this process significantly requires more labor-intensiveness, forged clubs are generally more expensive than cast clubs.
However, since the steel material used in forging is much softer with its carbon content, it can offer a better “feel.”
Manufacturing Process Sequence
Large golf club manufacturers use computer-aided and high-automated machinery. Meanwhile, small companies who specialize in customized clubs typically hand-make each club.
While the manufacturing process sequence is unique from one company to another, here is the typical progression for machine-made clubs.
Forming the Head
- Using CAD software, a designer would plan and create the head’s overall look and design.
- A mold is produced based on the computer-made design.
- The craftsmen insert the mold into a wax injecting molding machine. Here, the boiling hot wax is transported into the opening of the mold, creating clubheads made of wax.
- The craftsmen would then check each part individually for flaws and blemishes. They use a nail file to smoothen the mold and remove excess particles of wax. Checking the mold for imperfections is essential as any bumps will also manifest on the final product.
- The wax club heads are melted onto a wax tree and dipped into quicksand. As the quicksand bonds to the wax, it forms a shell around the mold’s outskirts.
- The wax tree is placed in a container and dries in a refrigerated room. This process undergoes five rounds before inserting the wax tree into a steam oven (1000 to 2000°F).
- After the wax residue vaporizes, the mold would be inverted. Then, they pour the molten metal onto the mold and wait for it to harden.
- Once the metal has cooled, they break the mold material from the tree.
- The craftsmen would then cut off each cast head.
- Finally, they treat the head by heating with a flame or induction oil to harden its surface.
Forming the Shaft
There are typically two ways to form the shaft:
- Tube Drawing: This is the process used for forming steel shafts. What happens is the craftsmen pull a tubed with desire length through an opening in a die. The die is usually smaller than the diameter of the tube. They repeat the process several times to draw the portion of the tub to neck down. After forming, they rely on a chrome-plated finishing.
- Pultrusion: This is the process used for forming graphite fiber-reinforced shafts. They pull a bundle of graphite fibers through a circular opening in a heated die. While doing that, they also force an epoxy resin through the same opening. The graphite fiber embeds in the epoxy as it hardens and forms the shaft. It will then be cooled and cut to its final length.
Assembling the club
- For metal shafts, the shaft is usually inserted into the hosel. They will then drill a small hole crossway where they will press a small metal pin. Finally, it is held in place with epoxy adhesive. For graphite shafts, they use adhesive to bond the shaft.
- After that comes the gripping process where a rubber grip wraps the upper shaft portion.
- Finally, they polish all the raised metal parts for its final appearance.
- Before putting it out, they place the adhesive stickers for the brand’s name and manufacturer and other information to the club. They either use paint or other finish to complete logos and letterings on the club.
Importance of Golf Club Specs
By now, you’re more well-equipped with how golf clubs are made.
Manufacturers follow very detailed specifications to make the best clubs in the market.
Each manufacturer pays much attention to the weight, angle, and overall design to ensure its quality and control.
More Information
Last Updated on December 4, 2023 by Paul Roger Steinberg